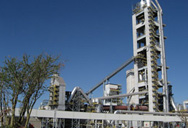
TYPES OF GRINDING PROCESS - Mechanical …
Cylindrical grinding process is mostly used to grind the surface of cylindrical object. Object will rotate around one axis and the surfaces of object which need to be grinded will be in concentric with that axis around which workpiece will rotate. Following figure shows the cylindrical grinding.
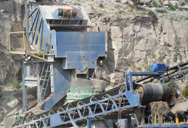
Frequent problems during grinding – grindaix …
Grinding is a widespread production process and has long been a fixed part of almost every industrial production environment. During grinding, the parts (workpieces) are literally given the “final polish”. Grinding operations thus contribute greatly to the quality of the finished workpiece.
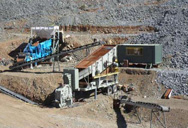
Basics of Grinding - Manufacturing
The Grinding Process Grinding is a material removal and surface generation process used to shape and finish components made of metals and other materials. The precision and surface finish obtained through grinding can be up to ten times better than with either turning or milling. Grinding employs an abrasive product, usually a rotating wheel brought into controlled contact with a work surface ...
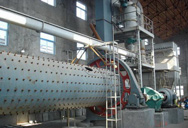
Grinding (abrasive cutting) - Wikipedia
Grinding is an abrasive machining process that uses a grinding wheel as the cutting tool.. A wide variety of machines are used for grinding: Hand-cranked knife-sharpening stones (grindstones)Handheld power tools such as angle grinders and die grinders; Various kinds of expensive industrial machine tools called grinding machines; Bench grinders
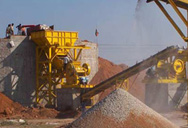
What is Grinding? - Definition from Corrosionpedia
13.06.2018 · Grinding is a subset of cutting, as grinding is a true metal-cutting process. Grinding is very common in mineral processing plants and the cement industry. Grinding is used to finish workpieces that must show high surface quality and high accuracy of shape and dimension. It has some roughing applications in which grinding removes high volumes ...
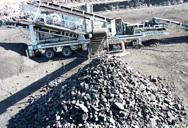
Grinding and Finishing - IIT Mechanical
grinding due to process-induced cracks • Diamond turning center can be used for non ferrous materials but it is a super-precision machine-tool (The equipment cost is ~ 20 crores besides the expensive operational cost) 1 . ME 338: Manufacturing Processes II Instructor: Ramesh Singh; Notes: Profs. Singh/Melkote/Colton Conformal Hydrodynamic Nanopolishing Process and Machine Process …
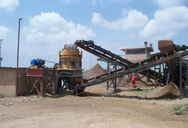
Grinding Machine: Types, Parts, Working & …
In this type of grinding process, the grinding wheel is maintained exactly the same shape as the final product. When the stone is passing through it automatically the pre-determined shape is formed on the workpiece. Wet and Dry grinding operation: Although there are two methods of doing a grinding operation, one is wet grinding and the second one is dry grinding. Wet grinding: In wet grinding ...
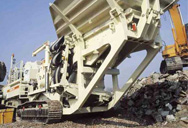
Grinding Process, Finish Machining, Aerospace …
New grinding process developments by Tyrolit, and machine tool developments by Makino, are changing that thought process. Utilizing new grinding techniques, incredible material removal rates up to 300 mm 3 /smm respective, 28 cubic inches per minute, and one inch of wheel width are being achieved. And, it is being done in the aerospace marketplace where the grinding of tough, nickel …
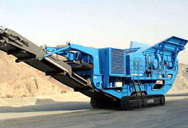
Grinding - LinkedIn SlideShare
Glazing makes the grinding face of the wheel smoother and that stops the process of grinding. • Sometimes grinding wheel is left ‘loaded’. • In this situation its cutting face is found being adhering with chips of metal. • The openings and pores of the wheel face are found filled with workpiece material particals, preventing the grinding action. • Loading takes place while grinding ...
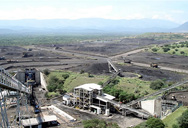
BASIC PRINCIPLE OF GRINDING - Mechanical …
Grinding process uses one abrasive tool to make controlled contact with workpiece surface. Normally grinding wheel is used as abrasive tool in process of grinding. Grinding wheel will have grains of abrasive materials and these grains of abrasive material will be termed as grit. Size of abrasive materials plays a very important role in grinding process as larger size grains will remove ...
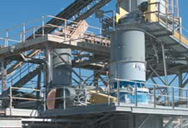
ANALYSIS OF PROCESS PARAMETERS FOR A SURFACE-GRINDING ...
assessment of the grinding-process quality usually inclu-des the micro-geometric quantities of the component. In order to predict the component behavior during the use or to control the grinding process, it is necessary to quantify surface roughness, which is one of the most critical quality constraints for the selection of grinding factors in a process planning. The process set-up often ...
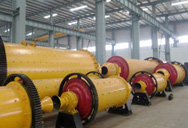
Chapter 5: Surface Grinder – Manufacturing …
The Surface Grinder is mainly used in the finishing process. It is a very precise tool which uses a stationary, abrasive, rotating wheel to shave or finish a metallic surface which is held in place by a vise. This vise, which is part of a table, or carriage is moved back and forth under the abrasive wheel. The surface grinder can cut steel in pieces no bigger than 18” long by 6” high by 8 ...
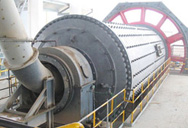
Metallographic grinding and polishing insight | …
This is normally the first step in the grinding process. Plane grinding ensures that the surfaces of all specimens are similar, despite their initial condition and their previous treatment. In addition, when processing several specimens in a holder, care must be taken to make sure they are all at the same level, or "plane," before progressing to the next step, fine grinding. To obtain a high ...
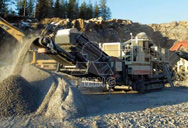
grinding - Deutsch-Übersetzung – Linguee …
grinding process n — ... tending to be flat with an offwhite colour when fully ripe; glumes adhering closely to the caryopsis; caryopsis characterised by abundant hairs on the apex, pronounced curvature and vitreous fracture; ...] light brown/amber colour, a specific defining characteristic that can be found [...] in all the products even after grinding. eur-lex.europa.eu. eur-lex.europa.eu ...
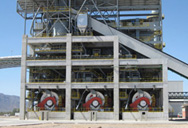
A Digital Twin for Grinding Wheel: An Information …
The methods for the abstraction of the production information from the manufacturer and the process information while grinding are presented. The development of a predictive model for redress life identification and computation of dressing interim period using spindle motor current data is developed and integrated. The quantifiable benefits from the digital twin for productivity and efficiency ...
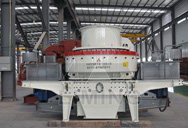
Wafer grinding, ultra thin, TAIKO - dicing …
Partial Wafer Grinding is an efficient grinding method to process broken or damaged wafers, or wafer sections. This technique can be employed to process wafers that had been damaged, or wafer sections that are still intact, thereby avoiding loss of the entire wafer material. Individual Die (Chip) Grinding . DGS processes individual dies that are already separated from the substrate. This is ...
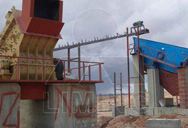
Precision Grinding - Bahmueller
Our experts take upstream and downstream processes into consideration, with the approach of integrated optimizations of your value-added processes. In advance of the grinding technology design, we arrange workshops with suppliers, process simulations and initial sample production, and specify the details of testing parameters together with you.
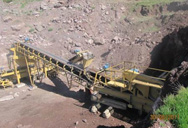
Electrochemical grinding - Wikipedia
Electrochemical grinding is a process that removes electrically conductive material by grinding with a negatively charged abrasive grinding wheel, an electrolyte fluid, and a positively charged workpiece. Materials removed from the workpiece stay in the electrolyte fluid. Electrochemical grinding is similar to electrochemical machining but uses a wheel instead of a tool shaped like the contour ...
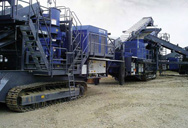
CNC grinding machines – grindaix GmbH
Dressing operations interrupt the grinding process and thus take place during non-productive time. View in the machining area of a CNC grinding machine for grinding crankshafts. The cooling of the process is realised with needle-nozzles by Grindaix GmbH. Image: EMAG GmbH & Co. KG CNC grinding applications. It is primarily those parts with stringent requirements in terms of dimensional and ...