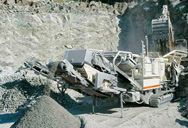
Cement mill - Wikipedia
A cement mill (or finish mill in North American usage) is the equipment used to grind the hard, nodular clinker from the cement kiln into the fine grey powder that is cement. Most cement is currently ground in ball mills and also vertical roller mills which are more effective than ball mills.
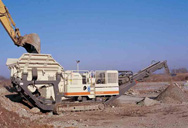
Cement Mill Grinding Media - Page 1 of 1
01.11.2017 · Cement Mill Grinding Media. Dear Experts, I want to know about the GM size wise percentage distribution in a 2 chamber close circuit OPC ball mill. Mill dim. 3.4 x 12.5. Media load 128 MT high chrome. Also let me know how do the supplier selected 80mm as max. Ball size in this mill? Please share the formula as well.
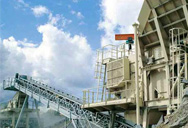
Energy-Efficient Technologies in Cement Grinding …
23.10.2015 · They are used in grinding of cement raw materials (raw meal) (i.e. limestone, clay, iron ore), cement clinker and cement additive materials (i.e. limestone, slag, pozzolan) and coal. Multi-compartment ball mills are relatively inefficient at size reduction and have high specific energy consumption (kWh/t).
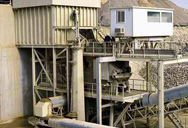
grinding media for cement mills - bandb …
Grinding media which is usually called as grinding balls are made up of high chromium steel. A cement mill is the comminution machine which is used to grind the hard and big sized clinker that comes from kiln section of cement industry into the fine optimal powder …
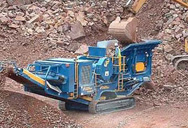
EFFECTS OF GRINDING MEDIA SHAPES ON BALL MILL …
media shape and mill power. The objective of this dissertation was to investigate how media shape affects grinding. Ball size distribution inside an industrial mill was analysed in terms of shapes and sizes. Load behaviour, mill power and breakage as affected by media shapes were studied in a pilot laboratory mill. An inductive proximity probe ...
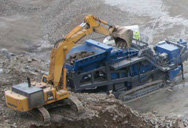
Effect of ball load and size distribution on …
01.12.2015 · Ball mills are known to be the highest energy consumers in cement grinding circuits. Inefficient grinding conditions prevail especially in the second compartments of multi-compartment cement grinding ball mills. Thus, energy efficient grinding mills such as high pressure grinding rolls (HPGRs), vertical roller mills (VRMs) and Horomill® etc. are introduced and integrated to the cement ...
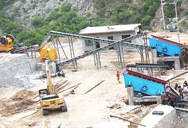
grinding media loading in cement grinding mill
Grinding Media Loading In Cement Grinding Mill Finish, A cement mill (or finish The grinding media and reduces energy consumption by 20-40% compared with a standard ball mill system Capacity of cement mills Mill (grinding) - Wikipedia Ball mills are commonly used in the manufacture of Portland cement and finer grinding stages SAG mills are autogenous mills but use grinding balls like a ball
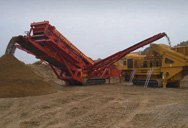
Grinding Media Ball - The Role of Media Ball in ...
25.07.2017 · Grinding Media Ball have a significant impact on the performance of grinding mills in terms of product size distribution, energy consumption and grinding costs. The below Figure shows main grinding costs for the specified mills. Considering the contribution of grinding media ball costs toward overall grinding costs, examining the possibility of minimizing them is worthwhile.
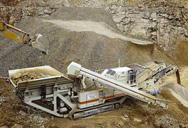
TYPES OF GRINDING MEDIA - energosteel.com
Cast iron grinding media — for the production this type of the grinding media used cast iron as «gray» and «white.» The ceramic grinding media — this type of the grinding media, as the name suggests, is made of ceramic and used mainly in small-sized mills (about 50 liters) in the stone and stone industries.
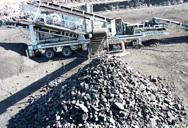
Mill (grinding) - Wikipedia
Ball mills are commonly used in the manufacture of Portland cement and finer grinding stages of mineral processing, one example being the Sepro tyre drive Grinding Mill. Industrial ball mills can be as large as 8.5 m (28 ft) in diameter with a 22 MW motor, [4] drawing approximately 0.0011% of the total worlds power (see List of countries by electricity consumption ).
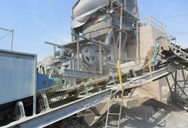
The effects of grinding media shapes on the …
01.02.2013 · The effect of the media shape on grinding kinetics of cement clinker in a ball mill was investigated. Results indicated that cement clinkers obey first-order breakage kinetics in the case of both balls and cylinders. The specific rate of breakage provided by cylinders is higher than that of balls. The results also showed that − 2.00 + 1.70 mm is an optimum feed size for 20 mm diameter balls ...
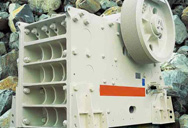
INVESTIGATION ABOUT THE EFFECT OF …
distribution, thus obtaining a finer and better performing cement. Grinding aids act at two levels: in the mill, with the reduction of cement coating on grinding media and mill lining, and in the separator, with the improvement of classification process. Detailed description of the use of grinding aids in cement industry is reported elsewhere [7].
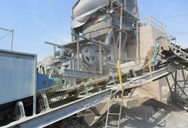
Cement Milling
Cement Milling. Cement milling is usually carried out using ball mills with two or more separate chambers containing different sizes of grinding media (steel balls). Grinding clinker requires a lot of energy. How easy a particular clinker is to grind ("grindability") is not always easy to predict, but large clusters of belite due to coarse silica in the feed are difficult to grind. Rapid ...
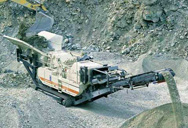
Grinding trends in the cement industry - Cement …
01.04.2010 · Summary: The main trends concerning grinding processes in the cement industry are still higher efficiency, reduction of the power consumption and system simplicity. In the case of new orders, vertical mills have increased their share to over 60 % and ball mills have fallen to less than 30 %. It is somewhat surprising that the number of different grinding processes and mill types used by the ...
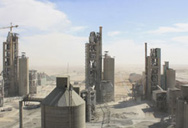
segregation of grinding media in mill - Popular …
Cement mill notebook - SlideShare. Jan 7, 2015 ... 3.2 Calculation of the Critical Mill Speed: G: weight of a grinding ball in ... liners 4.2.2 Classifying Mill Linings (Segregation Lining): The basic... Read More. Cylpebs grinding media segregation inside grinding mill - Grinding ... May 23, 2016 ... The smaller cylpebs have all migrated towards the feed side of the mill, and the larger ...
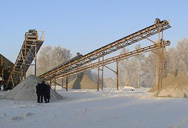
Grinding Media & Grinding Balls | Union Process, …
Silicon Carbide Balls are very high-cost grinding media that are used for milling same materials (silicon carbide ball to mill silicon carbide materials) to avoid contamination. They are only available in 5mm,10mm, 15mm and 20mm sizes. They are a special order item.
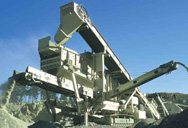
Effect of grinding aids in cement grinding
in a laboratory mill. As discussed in the literature [1,2,4], there was significant effect of using grinding aid in cement grinding. Grinding aids are active surface agents that counteract the agglomeration of very fine particles on the grinding media, thus inhibiting the grinding …
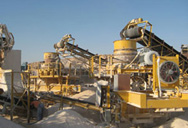
INCREASING OUTPUT OF CEMENT GRINDING IN BALL MILL- CASE …
increases production of cement mill. To seal air leakage in SKS Separator with uniform air gap increases output of cement mill. Proper distribution of grinding media with appropriate sizes also enhanced productivity of cement mill. Target- To increase the TPH from 190 to 220 TPH (PPC) with maintaining quality parameter i.e. 8% residue on +45 micron
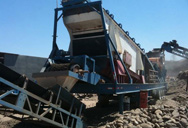
Prime Cement inaugurates grinding plant in …
02.09.2020 · Germany-based Loesche installed a Loesche Jumbo CCG (Compact Cement Grinding plant) with type LM 30.2 mill at the site. The cement plant is owned by Milbridge Holding, a group of companies involved in manufacturing and distribution of construction materials in Angola, the UAE, Rwanda and South Africa. It employs 110 workers directly.