
how to estimate the wear rate for Ball mill - Page …
08.12.2009 · Ball wear can be measured by weighing an entire charge before and after grinding a known tonnage of materials. With new balls sample of given size can be weighed before and after grinding a given tonnage and, assuming uniform wear per unit …
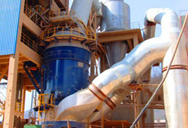
how to estimate the wear rate for ball mill
2009-12-8 Re: how to estimate the wear rate for Ball mill. Most practical way to by measuring empty height and calculating the % volumetric filling of grinding media.Alternative way to make track of mill main drive kW consumption reduction and add makeup charge according to
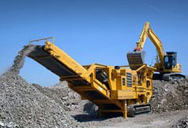
Re: how to estimate the wear rate for Ball mill - …
09.05.2009 · Re: how to estimate the wear rate for Ball mill. Dear Mr. Bhandari, I have developed software to calculate best pattern for material you want to grind. Kotiyal. Reply. Know the answer to this question? Join the community and register for a free guest account to post a reply.
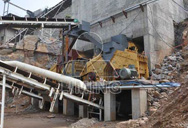
Re: how to estimate the wear rate for Ball mill - …
02.12.2011 · Re: how to estimate the wear rate for Ball mill. Guys its so easy you can do this by your self instead of begging some one mostly he never send that for you all ,, - First grinding media size for example 20 mm - Final size ex .. 100 mm - Estimate the wear rate and that is mostly for cement mills application = 35 g / ton Clinker
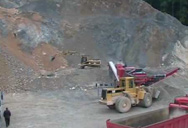
Re: how to estimate the wear rate for Ball mill - …
06.02.2011 · Re: how to estimate the wear rate for Ball mill. As per the experience, for 3 chambers 1000 HP cement mill, the given below thumb rule of wear rate and Kwh was found to be practicle.

(PDF) A comparison of wear rates of ball mill …
A comparison of wear rates of ball mill grinding media.pdf Journal of Mining and Metallurgy, 52 A (1) (2016 ) 1 - 10 # Corresponding author : [email protected]
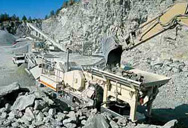
Rubber Ball Mill Liner Wear Rate Estimation - …
To participate in the 911Metallurgist Forums, be sure to JOIN & LOGIN Use Add New Topic to ask a New Question/Discussion about Grinding. OR Select a Topic that Interests you. Use Add Reply = to Reply/Participate in a Topic/Discussion (most frequent). Using Add Reply allows you to Attach Images or PDF files and provide a more complete input. Use Add Comment = to comment on someone else’s ...
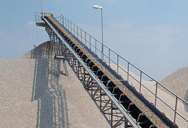
Optimization of mill performance by using
As the ball wear rate depends directly on the surface of the media charge, a small variation in power will lead to an important increase of wear rate. The risk of underloading or overloading the mill is an additional factor. A direct measurement of the ball level in the mill, more accurate than power readings, as well as a control of it, is
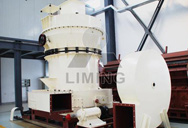
Grinding Media Wear Rate Calculation in Ball Mill
Table of ContentsData on Ball ChargesBall Mill Ball Wear ProjectionRecapitulation of Ball Wear FormulasPractical Application of Theoretical Conclusions In the previous discussion the fact was established that the work done by a ball when it strikes at the end of its parabolic path is proportional to its weight and velocity; then, since the velocity may be considered as constant for all the ...

Using Abrasion Index for calculating Steel Balls …
To participate in the 911Metallurgist Forums, be sure to JOIN & LOGIN Use Add New Topic to ask a New Question/Discussion about Grinding. OR Select a Topic that Interests you. Use Add Reply = to Reply/Participate in a Topic/Discussion (most frequent). Using Add Reply allows you to Attach Images or PDF files and provide a more complete input. Use Add Comment = to comment on someone else’s ...
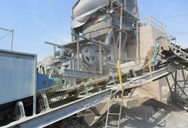
Ball Mill Liner Wear Rate Tracking Software-ball Mill
Ball mill liner wear rate tracking software ball mill liner wear rate tube mill internals liners feed end liners tube mill internals the xclass concept is a 2nd compartment ball mill liner including 2 plates each of one low media and liner wear rate increased mill ball mill liner wear rateball mill liner wear rate tracking softwareball mill liner wear rate tracking software clinker . More ...
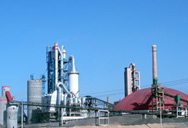
How to Size a Ball Mill -Design Calculator & …
15.05.2015 · A) Total Apparent Volumetric Charge Filling – including balls and excess slurry on top of the ball charge, plus the interstitial voids in between the balls – expressed as a percentage of the net internal mill volume (inside liners). B) Overflow Discharge Mills operating at low ball fillings – slurry may accumulate on top of the ball charge; causing, the Total Charge Filling Level to ...
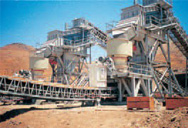
A discussion on the measurement of grinding …
01.07.2016 · The volumetric theory of ball wear states that the wear rate of a ball is proportional to its mass and, therefore, it is also proportional to the cube of its diameter (that is, to its volume). The origin of this theory considers that most comminution events result from impact mechanisms–which do not occur in laboratory mills, given their reduced diameter as compared to industrial mills. In ...
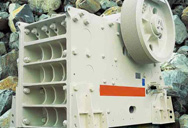
Ball Mill Design/Power Calculation
The basic parameters used in ball mill design (power calculations), rod mill or any tumbling mill sizing are; material to be ground, characteristics, Bond Work Index, bulk density, specific density, desired mill tonnage capacity DTPH, operating % solids or pulp density, feed size as F80 and maximum ‘chunk size’, product size as P80 and maximum and finally the type of circuit open/closed ...

Study on Tool Wear In-Process Estimation for Ball …
This stone introduces a method for in-process tool wear estimation of an air turbine spindle, which is equipped with a rotation control system for ultra-precision milling. Previous investigations revealed that the pressure of the compressed air for supply that is used to control the rotational speed and tool wear at the time when steady wear occurs, maintains a linear relationship when ...
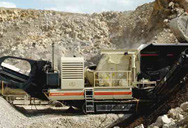
ball mill grinding media wear rate calculation
How Can i calculate the wear rate of grinding media in ball mills ... Apr 17, 2011 ... How Can i calculate the wear rate of grinding media in ball mills without having to go inside the mills and do the physical measurements. More details » Get Price. Abrasive and impactive wear of grinding balls in rotary mills - saimm . Apr 4, 1986 ... The wear of grinding balls by impace in a mill is not ...
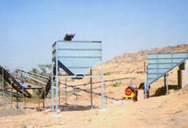
Determining The Wear Rate On Balls In A Ball Mill
Determining The Wear Rate On Balls In A Ball Mill. Dolomite use concrete crushed dolomite for the glass industry quarry grinding plant the use of crushed dolomite in glass industry more crushed limestone cost per ton for float glass what is the price of crushed glass per ton in south price per ton manufacturers amp price per ton glass recycling process for construction use
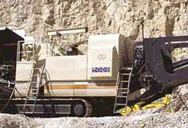
Optimum choice of the make-up ball sizes for …
01.09.2013 · Further, the ball size distribution in the mill is not a simple parameter that can be controlled directly, as it depends on the make-up ball charge and wear rate. Therefore, the industrial practice of determining the make-up ball sizes comes down to experience. However, there is a great deal of information that describes the variation of the grinding kinetics with the ball size and the ball ...
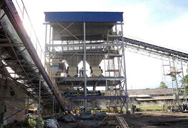
How to Reduce the Wear of Steel Ball in the Ball …
When the rotation speed of the ball mill machine reaches a certain degree, the filling rate is large, and the impacting times of steel ball on the material are more, the grinding area is large and the wear is fast. In addition, the too-high filling rate will change the movement state of the steel ball in the ball mill machine, reduce the impact effect on the large particle material. On the ...
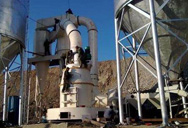
Ball mill - Wikipedia
Less wear takes place in stone lined mills. The length of the mill is approximately equal to its diameter. The general idea behind the ball mill is an ancient one, but it was not until the industrial revolution and the invention of steam power that an effective ball milling machine could be built. It is reported to have been used for grinding flint for pottery in 1870. Working. In case of ...