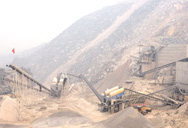
Ball Mill Design/Power Calculation
The basic parameters used in ball mill design (power calculations), rod mill or any tumbling mill sizing are; material to be ground, characteristics, Bond Work Index, bulk density, specific density, desired mill tonnage capacity DTPH, operating % solids or …

Grinding Ball Design - Metallurgist & Mineral Processing ...
Grinding balls are essential mechanical components in ball and semiautogenous (SAG) mills. Their function is crushing and grinding ore rocks weighing up to 45 kg (100 lb) preparatory to recovery of valuable minerals, from lead through rare earth elements, …
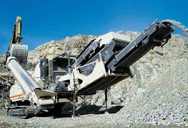
Ball mills - liming
With more than 100 years of experience in ball mill technology, liming’s ball mills are designed for long life and minimum maintenance. They grind ores and other materials typically to 35 mesh or finer in a variety of applications, both in open or closed circuits.

AMIT 135: Lesson 7 Ball Mills & Circuits – Mining Mill ...
Ball Mill Design A survey of Australian processing plants revealed a maximum ball mill diameter of 5.24 meters and length of 8.84 meters (Morrell, 1996). Autogenous mills range up to 12 meters in diameter. The length-to-diameter ratios in the previous table are for normal applications.
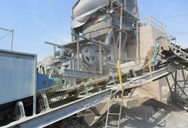
Grinding Ball Mill Design - Ball Mill
Mill type overview three types of mill design are common the overflow discharge mill is best suited for fine grinding to 75 106 microns the diaphram or grate discharge mill keeps coarse particles within the mill for additional grinding and typically used for grinds to 150 250 microns the centerperiphery discharge mill has feed reporting from both ends and the product discharges
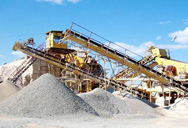
Ball mill Superior cement quality, More fl exibility ...
Proven mill design Buying a new mill is a huge investment. With over a century of ball mill experience and more than 4000 installations worldwide, rest assured – we have the expertise to deliver the right solution for your project. Our ball mill is based on standard modules and the highly flexible design can be adapted to your requirements.

open circuit to close circuit ball mill design in india ...
Ball Mill Design/Power Calculation. The basic parameters used in ball mill design (power calculations), rod mill or any tumbling mill sizing are; material to be ground, characteristics, Bond Work Index, bulk density, specific density, desired mill tonnage capacity DTPH, operating % solids or pulp density, feed size as F80 and maximum...
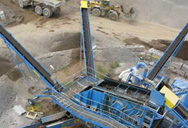
Ball mill - Wikipedia
A ball mill, a type of grinder, is a cylindrical device used in grinding (or mixing) materials like ores, chemicals, ceramic raw materials and paints.Ball mills rotate around a horizontal axis, partially filled with the material to be ground plus the grinding medium. Different materials are used as media, including ceramic balls, flint pebbles, and stainless steel balls.
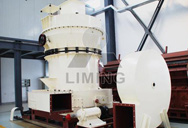
(PDF) DESIGN AND FABRICATION OF MINI BALL MILL- …
mini ball mill, a ball mill base is design and fabricate to withstand the weight of the rotating ja r, motor and gears. After a few hou rs, stop the mini ball mill and the powder can b e filtered...
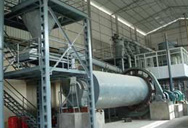
Design, Construction and Performance Analysis of a 5 ...
starting material (rock, ore, etc.) and the grinding ball media (balls), the milling process takes place. The milling process occursduring rotation as a result of the transfer of kinetic energy of the moving grinding media into the grinding product. The design of a ball mill can vary significantly depending on the size of the required mill, the

SAG mills (semi-autogenous grinding mills) - liming
SAG mills are also an optimum solution for wet grinding since crushing and screening in these cases can be difficult, if not impossible. Efficiency through automatic operation liming’s process engineers will assist you in creating an efficient software-driven process, from circuit design to start-up and optimization, to ensure you get your ...

Optimization of mill performance by using
The complete grind-out is required to obtain the accurate ball load measurement or the percentage by volume of balls in the mill. This is usually performed soon after a crash stop. The basic principle is to measure the height ‘H’ from the charge to the shell and the internal mill diameter ‘Di’.
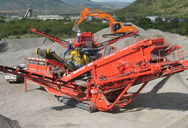
Ball Mill Design/Power Calculation - LinkedIn
Dec 12, 2016 · The basic parameters used in ball mill design (power calculations), rod mill or any tumbling mill sizing are; material to be ground, characteristics, Bond Work Index, bulk …
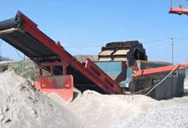
(PDF) Grinding in Ball Mills: Modeling and Process Control
Grinding in ball mills is an important technological process applied to reduce the size of particles which may have different nature and a wide diversity of physical, mechanical and chemical...

Mill (grinding) - Wikipedia
SAG is an acronym for semi-autogenous grinding. SAG mills are autogenous mills that also use grinding balls like a ball mill. A SAG mill is usually a primary or first stage grinder. SAG mills use a ball charge of 8 to 21%. The largest SAG mill is 42 (12.8m) …
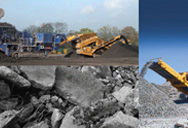
Ball Mills | Industry Grinder for Mineral Processing ...
Jan 30, 2018 · Ball mill, also known as ball grinding machine, a well-known ore grinding machine, widely used in the mining, construction, aggregate application. JXSC start the ball mill business since 1985, supply globally service includes design, manufacturing, …