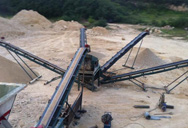
Grinding efficiency. Ball mill | by A.Sen | Aug, 2020 …
Closed circuit grinding system focuses on feed material characteristics, grinding progress in the mill, mill ventilation, classification and controls. The main trends concerning grinding processes ...
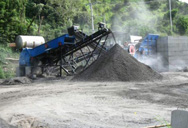
EFFECTS OF GRINDING MEDIA SHAPES ON BALL MILL …
grinding. Ball size distribution inside an industrial mill was analysed in terms of shapes and sizes. Load behaviour, mill power and breakage as affected by media shapes were studied in a pilot laboratory mill. An inductive proximity probe, light emitting diode, phototransistor and video photographs were used to determine the load orientation in terms of toe and shoulder positions. A load beam ...
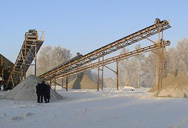
Ball mills | PSP Engineering
Ball mills for wet grinding. Ball mill grinding plants for wet grinding are mostly used in cases where subsequent processing requires material in the form of sludge. Whether it concerns treatment of ores for subsequent flotation processing or preparation of lime sludge for wet desulphurization… More info
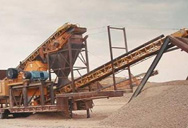
5 Ways To Improve Grinding Efficiency Of Ball …
26.12.2017 · According to Bond (1954), the grinding efficiency of a mill depends on the ball mill diameter, size of the media and mill speed. Ball mills with different length to diameter ratios for a particular power rating will produce different material retention times. The longer units are used for high retention ratios while shorter units are used where overgrinding is a factor to be considered.
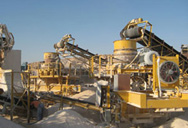
Grinding Media & Grinding Balls | Union Process, …
Silicon Nitride Balls are very high-cost grinding media that are used for milling same materials (silicon nitride ball to mill silicon nitride materials) to avoid contamination. They are now available in 2mm and 3mm and sizes up to 25mm. They are a special order item.

Grinding Mills/Ball Mills/Ball Grinder/Ball Mill …
Grinding ball can grind various ores and grindable materials in wet or dry way. - Ball mills have many types, generally including dry grinding mills, wet grinding mills, industrial grinding machines, and etc. - Grinding miller of our company has a novel structure and stable performance.
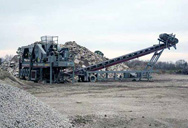
OUTOTEC MH SERIES GRINDING MILLS
Outotec® MH Series Grinding Mills offer a cost-effective, and easy to operate and maintain grinding solution across the mill lifecycle. The MH Series includes a range of SAG, ball, and rod mills in standardized sizes with a capacity of up to 3.1 MW installed power, and is based on over 100 years of experience with grinding technologies.

Calculate and Select Ball Mill Ball Size for …
In Grinding, selecting (calculate) the correct or optimum ball size that allows for the best and optimum/ideal or target grind size to be achieved by your ball mill is an important thing for a Mineral Processing Engineer AKA Metallurgist to do. Often, the ball used in ball mills is oversize “just in case”. Well, this safety factor can cost you much in recovery and/or mill liner wear and ...

Grinding · Christian Pfeiffer
Ball mills; Compact mills; Roller presses; Vertical mills; Diaphragms, mill shell linings and grinding balls; Our Service 360°MillCheck Grinding plants for your industry Cement industry Coal grinding Minerals industry Mining and wet grinding Separation. Back. Learn more Optimizing separation processes; Good mills deliver good results. But a separator enables you to achieve even better …
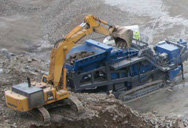
Grinding Mills | Westpro Machinery
Grinding Mills. Westpro’s heavy duty grinding mills are designed for durability and excellent grinding performance in mining applications. 6ft Diameter x10ft Ball and Rod Mills at the Westpro Shop ADVANTAGES. Sizes up to 4.9m (16tf) diameter and 4500hp (3356KW) Available with rubber, steel or ceramic liners; APPLICATIONS. Size reduction of ...
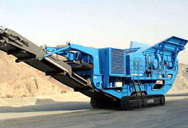
Mill (grinding) - Wikipedia
SAG is an acronym for semi-autogenous grinding. SAG mills are autogenous mills that also use grinding balls like a ball mill. A SAG mill is usually a primary or first stage grinder. SAG mills use a ball charge of 8 to 21%. The largest SAG mill is 42 (12.8m) in diameter, powered by a 28 MW (38,000 HP) motor.
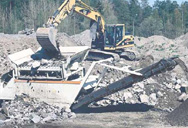
STANEX diaphragm for ball mills - flsmidth-prod-cdn ...
STANEX diaphragm for ball mills Benefits Highest possible grinding capacity due to narrow build-in length - one of the shortest build-in length of any diaphragm on the market • Longer effective chamber lengths and better use of the mill length • Frees up space for more material which leads to a production increase Large free flow area optimises production rate • Low pressure drop across ...
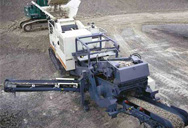
Large Batch Laboratory Rod Mill / Ball Mill - …
The 21 Liter (5 gallon) 911METALLURGY 911MPE21BM dual function Laboratory Rod Mill / Ball Mill is designed to meet the industrial requirements to grind coal, cement and a wide variety of ores. The dual duty Laboratory Grinding Mill consists of a gear motor mounted on a high precision solid steel underframe complete with outlet funnel and a set of separation screens plus sample collector. A ...
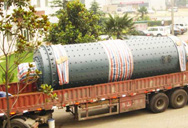
Mill equipment · Christian Pfeiffer
Diaphragms, mill shell linings and grinding balls. The efficiency of ball mills can be significantly increased by the quality of your components. For this reason Christian Pfeiffer continues to develop their mill components, enriching the market again and again with their innovations. In the process, the focus is on high functionality and wear resistance together with low specific energy ...
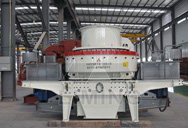
Ball mill for cement making plant, ball mill works ...
22.05.2014 · The ball mill is a key equipment to grind the crushed materials, and the ball mill is widely used in powder-making production line including cement, silicate, new-type building material ...
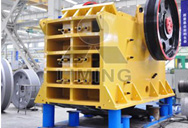
calculates the grinding charge of a ball mill | …
SAG Mill product P80 values are typically in the range of … OPTIMIZING SAG MILL PRODUCT SIZE IN SAG MILL _ BALL MILL GRINDING CIRCUITS. How Can i calculate the wear rate of grinding media in ball … How Can i calculate the wear rate of grinding media in ball mills without having to go inside the mills and do the physical … how to calculate the mill charge ? grinding media charge ...
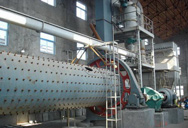
Grinding trends in the cement industry - Cement …
Summary: The main trends concerning grinding processes in the cement industry are still higher efficiency, reduction of the power consumption and system simplicity. In the case of new orders, vertical mills have increased their share to over 60 % and ball mills have fallen to less than 30 %. It is somewhat surprising that the number of different grinding processes and mill types used by the ...