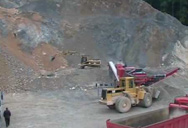
Iron Ore Magnetic Separation Process
Magnetic separation process of iron ore . Besides, the separation machines are devide into the dry and wet magnetic separation. generally, iron ore with an iron content of 35 can increase iron content by 20 after magnetic separation. such a combined process method, the ore utilization rate can reach 90. in the process of magnetic separation, it saves water, reduces cost and pollution.
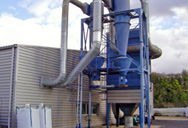
Magnetic Separation and Iron Ore Beneficiation – …
Magnetic separator separates the iron ore feed material into two or more components. If the purpose is to produce a magnetic concentrated iron ore then the other component which is non-magnetic is the tailings. In some cases there can also be a possibility of separating the less magnetic third component which is called middlings. Each of these material streams are to be transported into, through the …
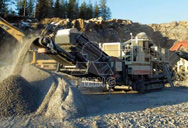
Magnetic separation - Wikipedia
Magnetic separation is the process of separating components of mixtures by ... The first pair of balls was weakly magnetized and served to draw off any iron ore present. The second pair were strongly magnetized and attracted the wolframite, which is weakly magnetic. These machines were capable of treating 10 tons of ore a day. Common applications. Magnetic separation can also be used in ...
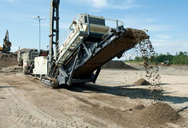
magnetic separation of iron ores - los-bonitos.ch
Iron Ore Magnetic Separation. Table of ContentsMagnetic Iron Ore ResourcesHistory of Development of Magnetic Separator Treatment Method DeterminationPresent Practice and State of DevelopmentWet Magnetic Separation of Cornwall OreDustLow Grade of ConcentratesResults of Dry Separation in Testing LaboratoryNo. 234, Separation Test on Jackson Hill Ore, Arnold, N. Y.Summary In the West, …
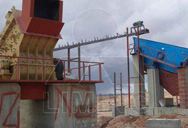
How magnetic separation optimizes sorting and …
If your DMS concentrate contains weakly paramagnetic and diamagnetic minerals (e.g, diamonds), a three-stage tiered magnetic separation process is ideal for sorting. Stage 1: A weak magnet and a high-belt speed – scalping process removes ferromagnetic material
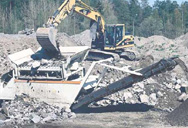
BENEFICIATION OF BOREHOLE IRON ORE SAMPLES THROUGH …
iron ore samples for upgrading by multi-stages magnetic separation technique. The main pa-rameters of the magnetic separation affecting the effectiveness of low intensity rougher stage and lower intensity cleaner stage as well as higher intensity scavenger stage were investigated. The interpretation of separability in terms of chemical
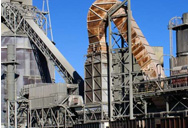
The Six Main Steps of Iron Ore Processing | …
When the iron ore is extracted from the mine, it must undergo several processing stages. Six steps to process iron ore. 1. Screening. We recommend that you begin by screening the iron ore to separate fine particles below the crusher’s CSS before the crushing stage. A static screen is used to divert the fine particles for crushing. This step prevents overloading the crusher and increases its efficiency.
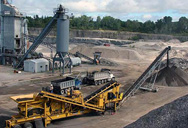
Dry Iron Ore Beneficiation | Iron Ore Separation - …
Magnetic separation is typically used in the beneficiation of high grade iron ores where the dominant iron minerals are ferro and paramagnetic. Wet and dry low-intensity magnetic separation (LIMS) techniques are used to process ores with strong magnetic properties such as magnetite while wet high-intensity magnetic separation is used to separate the Fe-bearing minerals with weak magnetic ...
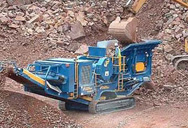
BENEFICIATION OF BOREHOLE IRON ORE …
Because of the fine dissemination of the iron minerals and the most abundant gangue mineral, the particles size of ore was set at 80% passing 150 meshes. Rougher tests of magnetic separation produced concentrates with iron content of about 58.2% Fe; the tailing of rougher stage was then scavenged using higher magnetic intensity. Further, the rough and scavenged concentrates were mixed and fed into a cleaner stage …
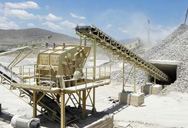
What Is Iron Ore Beneficiation? (with pictures)
09.05.2020 · Methods such as screening, crushing, and grinding of iron ore are often used in various ways to purify it, along with several stages of magnetic separation. Raw iron ore has to be purified for use. The iron ore industry classifies the material by the concentration of the metal that is present after iron ore beneficiation has been completed. High-grade iron ore must have a concentration of 65% iron or …
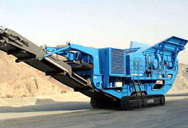
Dry Magnetic Separation of Iron Ore of the ...
The sequence of the separation process corresponded to the method 13 and was as follows: the sample of iron ore (60 g) was fed into the working area of the device and in the magnetic field was divided into the magnetic and nonmagnetic components. After the separation cycle at a given current strength in the winding the magnetic concentrate was weighed on laboratory scales and returned to the original sample…
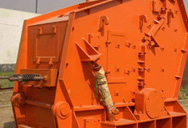
Mineral processing - Wikipedia
Magnetic separation is a process in which magnetically susceptible material is extracted from a mixture using a magnetic force. This separation technique can be useful in mining iron as it is attracted to a magnet. In mines where wolframite was mixed with cassiterite, such as South Crofty and East Pool mine in Cornwall or with bismuth such as at the Shepherd and Murphy mine in Moina, Tasmania, …
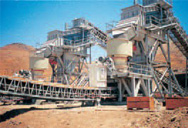
Processing of Lean Iron Ores by Dry High …
Magnetic separation of the roasted ore resulted in significant enrichment of the ore with respect to iron. The optimized parameters for reduction roasting were 13 mm particle size, 60 min roasting ...
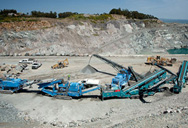
Developments in the physical separation of iron …
01.01.2015 · This chapter introduces the principle of how low-grade iron ores are upgraded to high-quality iron ore concentrates by magnetic separation. Magnetite is the most magnetic of all the naturally occurring minerals on earth, so low-intensity magnetic separators are used to upgrade magnetite ores. On the other hand, because oxidized iron ores like martite, hematite, specularite, …