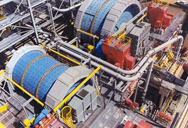
Iron processing | Britannica
Study the production and structural forms of iron from ferrite and austenite to the alloy steel Iron ore is one of the most abundant elements on Earth, and one of its primary uses is in the production of steel. When combined with carbon, iron changes character completely and becomes the alloy steel.
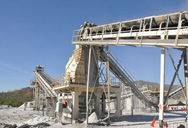
Must-know: The basics of iron ore - …
17.07.2014 · Total production of iron ore is about two billion metric tons. Australia and Brazil dominate the seaborne trade—iron ore is shipped to other countries—with a 72 % …
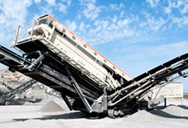
basic production of iron from ore - lessbutmore.nl
Top Iron. basic production of iron from ore. Iron Production - Chemistry LibreTexts. The production of iron from its ore involves an oxidation-reduction reaction carried out in a blast furnace. Iron ore is usually a mixture of iron and vast quantities of impurities such as sand and clay referred to as gangue. The iron found in iron ores are ...
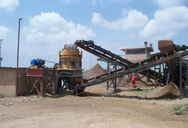
Iron Ore Processing for the Blast Furnace
Creating steel from low-grade iron ore requires a long process of mining, crushing, separating, concentrating, mixing, pelletizing, and shipping. The process of mining low -grade iron ore, or taconite, requires massive resources. Heavy industrial mining equipment, expansive mines, and a skilled labor pool are all required.
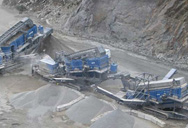
Iron - Wikipedia
Iron (/ ˈ aɪ ər n /) is a stone element with symbol Fe (from Latin: ferrum) and atomic number 26. It is a metal that belongs to the first transition series and group 8 of the periodic table.It is by mass the most common element on Earth, forming much of Earths outer and inner core.It is the fourth most common element in the Earths crust.. In its metallic state, iron is rare in the ...
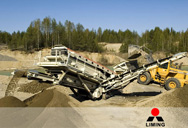
Global iron ore production by region 2018 | Statista
Production of iron ore worldwide by region 2018 Published by M. Garside, Jul 7, 2020 This statistic shows the production of iron ore worldwide in 2018 by region. In that year, some 904.6 million...
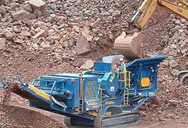
Steps in the Modern Steelmaking Process
21.08.2020 · Two processes, basic oxygen steelmaking (BOS) and electric arc furnaces (EAF), account for virtually all steel production. Ironmaking, the first step in making steel, involves the raw inputs of iron ore, coke, and lime being melted in a blast furnace.
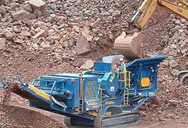
Iron Production - Chemistry LibreTexts
The production of iron from its ore involves an oxidation-reduction reaction carried out in a blast furnace. Iron ore is usually a mixture of iron and vast quantities of impurities such as sand and clay referred to as gangue. The iron found in iron ores are found in the form of iron oxides.
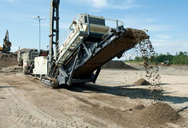
88 IRON ORE - USGS
The share of steel produced by basic oxygen furnaces, the process that uses iron ore, continued to decline from 37.3% in 2015 to an estimated 30% in 2019 owing to increased use of electric arc furnaces because of their energy efficiency, reduced environmental impacts, and the ready supply of scrap.
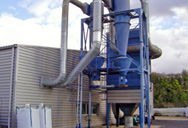
Global Production and Consumption of Iron Ore | …
10.05.2012 · For these reasons, iron ore production is concentrated in the hands of a few major players. World production averages two billion metric tons of raw ore annually. The world’s largest producer of iron ore is the Brazilian mining corporation Vale, followed by …
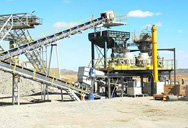
Steelmaking and Refining | Introduction to …
The HIsarna steelmaking process is a process of primary steelmaking in which iron ore is processed almost directly into steel. The process is based on a new type of blast furnace called a Cyclone Converter Furnace, which makes it possible to skip the process of manufacturing pig iron pellets, a necessary step in the basic oxygen steelmaking process. Because it skips this step, the HIsarna ...
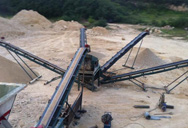
Australia - iron ore production volume 2018 | …
In the 2018 fiscal year, over 53 gigatons of iron ore were produced in Australia, an increase from the previous year.
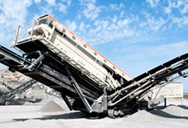
production of steel & iron ore requirements
For producing one tonne of crude steel, 1.6 tonnes of iron ore consumption has been assumed. If we add iron ore requirements of RINL of about 5.00MT (3.13 MT x 1.6 tonnes), the total iron ore requirements from non-captive mines work out to 58.31MT or about 60MT.
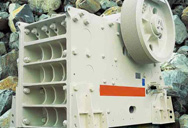
Extraction of Iron | Metallurgy | Blast Furnace and …
Wrought iron is the purest form of iron available commercially available and is prepared from cast iron by heating cast iron in a furnace lined with Haematite (Fe2O3). The Haematite reacts with Carbon in the cast iron to give pure iron and carbon monoxide gas which escapes. Limestone is …
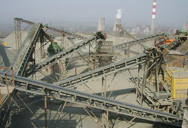
Iron Extraction Process - Dillinger
At the bottom of the furnace the iron ore is chemically reduced. The blast reacts with the coke; carbon dioxide and carbon monoxide are formed at temperatures of up to 2000 °C. The carbon monoxide removes the oxygen from the iron ore resulting in pig iron production. Slag is formed from the other ore components and the additions. Casting bay. The hot metal is filled into torpedo cars via the ...