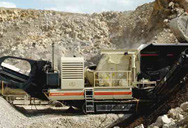
Heat Balance Sheet For Raw Mill - …
Heat Balance Sheet For Raw Mill. India is the second largest producer and consumer of rice in the world. Modernization of rice mill yield more rice from it, and came with more competition between the rice mill entrepreneurs. It involve of high capital, and huge investment to start a new rice mill. Even though more rice mills were emerged in southern region of India. Whatever your requirements ...
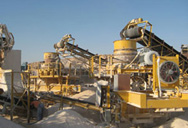
FOR CEMENT RAW MATERIAL - loesche.com
In the 1930s Loesche mills are used to grind cement raw material for the first time. The major breakthrough came at . the start of the 1960s when rotary kilns with heat exchang - ers (dry process) are introduced. The following Loesche technological features make the deployment of these mills so successful in the cement industry: • Low specific energy consumption • Low pressure loss through ...
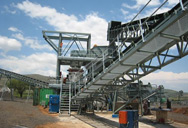
How To Calculate False Air In Ball Mill
Ball mill heat balance calculation in process engineering.Calculation of the power draw of dry multi-compartment ball mills.May 6, 2004 , key words power draw, cement, dry grinding, ball mill , electricity consumption for cement production is used for grinding the raw material , 16 billion tons and the grinding process consumes nearly 2 of the electricity produced , hacettepe university.
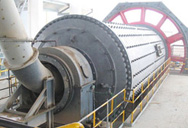
cement raw mill - Deutsch-Übersetzung – Linguee Wörterbuch
Viele übersetzte Beispielsätze mit "cement raw mill" – Deutsch-Englisch Wörterbuch und Suchmaschine für Millionen von Deutsch-Übersetzungen.
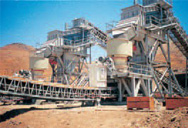
Raw Mill Feeding - Cement Plant Optimization
Mill Feeders: Feeders for raw mills will be directly installed under hoppers with rod gate in between. The feeders are generally 2 to 3 m long and discharge on to a common conveyor which will take feed to mill. Feeders for mills meter feed rates and also totalize tons fed. For raw mill feeding, table feeders, belt feeders, and weigh feeders have been used. However, weigh feeders are the most ...
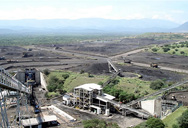
WPU replacement in Mexico Gearbox replacement on a ...
ones replaced the gearboxes of a horizontal cement mill and a horizontal raw mill in 1993. Both new gearboxes were of CPU type. The latest installation was a WPU type gear unit for another vertical raw mill in 2005. Cementos La Cruz Azul also encountered problems with the gearbox of a Polysius roller mill type RM/46/26 for raw grind-ing, designated as mill No. 5. The gearbox of this mill had ...
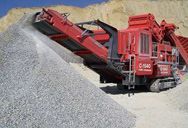
Heat Integration in a Cement Production | …
20.10.2017 · There are two operation modes of the particular cement factory. The first one is when the raw mill is under operation and, in this case, the cooling water flowrate at the cooling tower is 3 t/h. A hot gas from the kiln is fed into the raw mill and a raw material is heated. The second operation mode presumes that the raw mill is out of operation ...
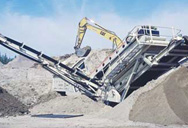
Raw Mill In Cement Plant,Cement Making Plant
This stone mainly introduces the raw mill in cement plant. In order to achieve the desired setting qualities in the finished product, a quantity (2-8%, but typically 5%) of calcium sulfate (usually gypsum or anhydrite) is added to the clinker and the mixture is finely ground to form the finished cement powder. This is achieved in a cement raw mill. The grinding process is controlled to obtain ...
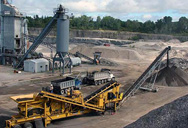
Best energy consumption - International Cement …
The most obvious area for attention is that of grinding, both raw and cement. In either case, grinding is, by design, a very inefficient process. Figure 2: breakdown of electrical energy consumption at a typical cement plant. Figure 3: vertical roller mill. The ball mill has been the industry’s workhorse for over a century and despite its estimated meagre four per cent efficiency, little has ...
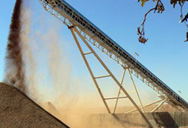
what is the raw mill in cement - ag18.ch
Raw Mill In Cement Plant,Cement Making Plant. This mainly introduces the raw mill in cement plant. In order to achieve the desired setting qualities in the finished product, a quantity (2-8%, but typically 5%) of calcium sulfate (usually gypsum or anhydrite) is added to the clinker and the mixture is finely ground to form the finished cement powder.

Material Handling In Raw Mill In Dry Cement …
finish mill packing cement bloomoonmedia. Aug 30 2012 Packing Shipping Cement Manufacturing Process Phase 1 Raw Material Extraction Cement uses raw materials that cover calcium silicon iron and aluminum Such raw materials are limestone clay and sand Limestone is for calcium It is combined with much smaller proportions of sand and clay Sand clay fulfill the need of silicon iron and aluminum
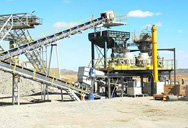
Manufacturing process | Lafarge - Cement, …
40% result from the combustion required to heat the cement kilns to 1500° Step 3: Raw meal drying, grinding, and homogenization: The raw mix, high grade limestone, sand, and iron ore are fed from their bins to raw mills, called air swept mills, for drying and fine grinding. The raw mill contains two chambers, separated by diaphragm, namely a drying chamber and a grinding chamber. The hot ...
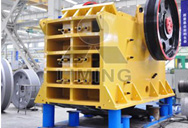
Difference Between Vrtical Raw Mill And Ball Mill …
Vertical Raw Mill Cement Capacity. A cement mill or finish mill in North American usage is the equipment used to grind the hard nodular clinker from the cement kiln into the fine grey powder that is cementMost cement is currently ground in ball mills and also vertical roller mills which are more effective than ball millsget price. Online consulting ; Grinding Pressure In Vertical Roller Mill ...
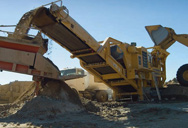
HARDTOP Gießereitechnologie GmbH - Cement
The raw material of modern construction cement is a mixture of lime stone and clay as well as corrective substances such as iron ore or sand. On their way from the quarry to the finished product, the materials undergo a large number of processing steps. The installations and equipment for the cement production need to meet strict requirements with regard to wear and heat resistance. For many ...
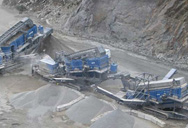
Cement Directory: Mill Internals
Cementrade is a supplier of grinding media, lining for cement, raw mills and heat resistant casting. Christian Pfeiffer Maschinen Fabrik GmbH. Christian Pfeiffer Beckum stands for innovation in the fieldof grinding technology and separator con ... CITIC Heavy Machinery Co. Ltd. CJSC Industry Service. CJT Surplus Equipment. Clair Engineers Pvt Ltd. CNBM International Engineering Co., Ltd. CNBM ...
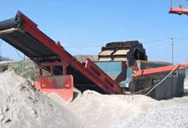
Cement Raw Material | Loesche
The LOESCHE scope of delivery includes a raw material mill with a capacity of 540 t/h of cement raw meal, a cement mill with an output of 350 t/h of clinker as well as a coal mill with an output of 45 t/h. VIEW MORE. Cement Raw Materials. The coordinates of the grinding table diameter and number of rollers can be read off from the table. The x-coordinate indicates which product throughputs can ...
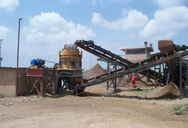
feeling density of raw mill of cement line
Long a popular material stone retains heat with-stands corrosion and resists fire. Because each unit is small—usually four inches wide and twice as long stone is an ideal . Read More; Cement Ball Mill Processing Site_ Heavy Industry . The cement plant cooperated with us in 2011 and purchased our jaw crusher. Small type ball mill equipment grinds raw material for fine processing. With the ...